In the rapidly evolving landscape of industrial automation, electric vehicle development, and precision engineering, the demand for advanced testing and control systems has never been greater. At the heart of this technological revolution lie specialized components such as hysteresis brakes, hysteresis dynamometers, hysteresis clutches, motor dynamometers, and integrated motor test systems. These solutions form the backbone of performance validation across industries ranging from aerospace to renewable energy. Let’s explore how these technologies work synergistically to redefine efficiency and accuracy in modern engineering applications.
UNDERSTANDING HYSTERESIS TECHNOLOGY: THE SCIENCE BEHIND THE MAGIC
Hysteresis-based devices operate on the principle of magnetic hysteresis loss, a phenomenon where energy dissipates as heat when magnetic materials undergo cyclic magnetization. This unique characteristic enables non-contact torque transmission and load control, eliminating mechanical wear while delivering unparalleled precision. Unlike traditional friction-based systems, hysteresis devices maintain consistent performance over extended periods, making them indispensable for applications requiring repeatable results.
HYSTERESIS BRAKES: THE UNSUNG HEROES OF CONTROLLED DECELERATION
Modern hysteresis brakes represent a quantum leap in motion control technology. These electromagnetic braking systems excel in scenarios demanding smooth, adjustable torque without physical contact between components:
- Precision tension control in semiconductor manufacturing
- Web handling systems for flexible electronics production
- Dynamometer absorption units for electric motor testing
- Robotic arm positioning in automated assembly lines
The absence of friction particles and lubricants makes hysteresis brakes particularly valuable in cleanroom environments, while their instantaneous response time (typically under 10ms) ensures precise control in high-speed applications.
BREAKTHROUGHS IN HYSTERESIS DYNAMOMETER DESIGN
Contemporary hysteresis dynamometers have transformed how engineers evaluate rotational systems. These advanced load banks provide:
1. Seamless torque adjustment from zero to maximum capacity
2. Bidirectional loading capabilities for regenerative system testing
3. Real-time energy recovery simulation for hybrid powertrains
4. Sub-1% torque linearity across entire operating ranges
Recent innovations incorporate adaptive cooling systems that maintain thermal stability during prolonged testing cycles, coupled with integrated torque/flux sensors that enable closed-loop control strategies.
THE EVOLUTION OF HYSTERESIS CLUTCHES IN SMART MANUFACTURING
Modern hysteresis clutch solutions address critical challenges in power transmission systems:
- Slip-controlled torque limiting for overload protection
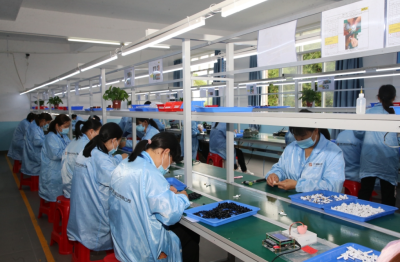
- Vibration damping in high-speed spindle applications
- Precision synchronization in printing press mechanisms
- Energy-efficient coupling in HVAC compressor systems
Advanced models now feature embedded IoT sensors that monitor coil temperatures, airgap distances, and magnetic flux density, enabling predictive maintenance and optimizing operational lifespans.
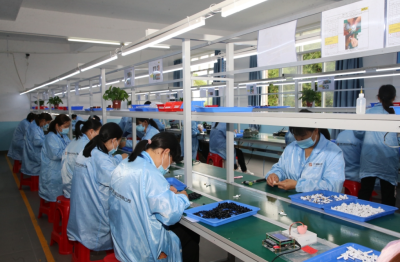
MOTOR DYNAMOMETERS: THE GATEKEEPERS OF ELECTRICAL MACHINE PERFORMANCE
State-of-the-art motor dynamometer systems have become critical tools for characterizing electric machines in the era of electrification. Key advancements include:
- Multi-axis torque measurement capabilities
- Regenerative grid simulation for V2G applications
- NVH (Noise, Vibration, Harshness) analysis integration
- AI-driven efficiency mapping algorithms
Modern systems support testing protocols for emerging technologies such as axial flux motors and superconducting rotors, with some platforms achieving rotational speed accuracies within ±0.002% of setpoint values.
INTEGRATED MOTOR TEST SYSTEMS: WHERE PRECISION MEETS AUTOMATION
Comprehensive motor test equipment now combines hysteresis loading technologies with sophisticated data acquisition systems to create turnkey testing solutions. A typical advanced system might incorporate:
- Programmable thermal cycling chambers
- Three-phase power analyzer modules
- Bearing friction characterization tools
- Electromagnetic compatibility (EMC) testing suites
These systems increasingly employ digital twin technology, allowing virtual simulation of test scenarios before physical execution, significantly reducing development cycles.
APPLICATION SPOTLIGHT: TRANSFORMING INDUSTRIES THROUGH ADVANCED TESTING
AUTOMOTIVE ELECTRIFICATION
Hysteresis-based dynamometer systems are crucial for validating EV powertrains, performing endurance tests on motors operating at 20,000 RPM or higher while maintaining torque measurement accuracies within 0.1% of reading.
AEROSPACE ACTUATOR TESTING
Compact hysteresis brakes enable precision load simulation in flight control systems, replicating aerodynamic forces with millisecond-level response times critical for next-gen fly-by-wire systems.
RENEWABLE ENERGY SYSTEMS
Specialized motor test benches equipped with hysteresis load banks validate wind turbine generators under simulated grid fault conditions, ensuring compliance with stringent grid code requirements.
MEDICAL DEVICE MANUFACTURING
Miniaturized hysteresis clutches provide sterile, particulate-free torque control in surgical robot assemblies, where reliability and precision directly impact patient outcomes.
THE DATA-DRIVEN FUTURE OF TESTING TECHNOLOGIES
Emerging trends in hysteresis-based test systems focus on enhanced connectivity and intelligent analytics:
- Cloud-based test protocol management
- Machine learning-assisted anomaly detection
- Digital thread integration across product lifecycles
- AR-assisted maintenance and calibration
These developments are creating smarter, self-optimizing test environments that reduce human intervention while improving data integrity.
SELECTING THE RIGHT SOLUTION: KEY CONSIDERATIONS
When specifying hysteresis-based test equipment, engineers should evaluate:
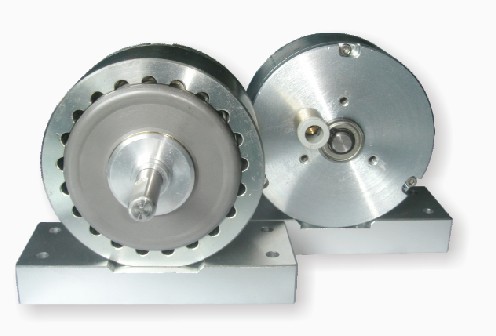
TORQUE RANGE AND CONTROL RESOLUTION
Ensure the system covers both starting and continuous torque requirements with adequate resolution for your application’s precision needs.
THERMAL MANAGEMENT CAPABILITIES
Assess cooling system efficiency, particularly for high-duty cycle operations or environments with restricted airflow.
CONTROL SYSTEM INTEGRATION
Verify compatibility with existing PLC architectures and communication protocols (CAN bus, EtherCAT, Modbus TCP/IP).
FUTURE-PROOFING FEATURES
Consider modular designs that allow for sensor upgrades or software enhancements as testing requirements evolve.
CONCLUSION: ENGINEERING TOMORROW’S INNOVATIONS TODAY
As industries push the boundaries of electromechanical system performance, hysteresis-based technologies and advanced motor testing solutions continue to provide the foundation for innovation. From enabling the mass production of efficient electric motors to ensuring the reliability of mission-critical aerospace components, these systems represent more than just test equipment – they are the guardians of quality in an increasingly electrified world.
By embracing the latest advancements in hysteresis brakes, dynamometers, and integrated test platforms, forward-thinking organizations can accelerate their R\u0026D cycles, improve product reliability, and ultimately deliver superior technologies to market. Motor performance analysis of precision engineering isn’t just about building better machines – it’s about creating smarter systems to test, validate, and perfect them.